There are many names for this device such as a self-balancing scooter, self-balancing two-wheeled board, segway or hoverboard. There is no universally accepted name for this device and I like hoverboard the best so I will go with that.
My video came out 2 days after Izzy's Adirondack chair.
I think we need to have a race. see his video here.

I am not ready to ride the hoverboard so I decided to make a hoverboard chair.
Making this hoverboard chair out of wood is will be very easy.
How to build
First we need a few measurements of the board. The middle measurement is needed to build the steering and the height will be for the chassis. These numbers will be used to help build the frame and and keep things level.
The steering
Plywood will be used for the steering. Two pieces of 3/4 inch plywood are cut to the shape shown below.
The two pieces can be glued together. After the glue is dried it can be sanded and the corners can be rounded.
A hole is drilled in the middle of the block, this will be for a carriage bolt.
1. Drill a hole first with a forstner bit the depth should be the same amount as the top head of the bolt.
2. Now drill a hole the same size a the thickness of the bolt.
3. Hammer the bolt head until it is buried in the wood.
The frame will be made of a couple of 2x4's. I picked some clean pieces from the lumber store with as few knots possible.
I found some wheels from a hand truck and since they had bearings they would work fine.
The hole in the wheels is 3/4 inch so I bought some 3/4 inch threaded rod. The rod was too large so I had to grind it down a bit. To do this I placed it in a cordless drill and turned it on the belt sander. It did not take very much and in no time it fit the wheel.
The rear end
A dado cut is made in a piece of 2x4 for the threaded rod. I cut it so the rod would fit tight in the slot. A pound with a fist will seat it perfectly.
The frame is coming together, I made a dado joint for the sides and a dovetail joint for the chassis. These are not necessary but look nice and are some what stronger. The other way is to just put some large screws.
I knew the width I would use by matching several chairs I had in the house but the length was different on the chairs.
After I decided which chair to use I was able to trim down the sides using a jigsaw.
Plywood is used to hold the threaded rod in the dado slot. The other side will be for the back of a chair.
For the other side of the bottom another piece of plywood is used. Flipped over this will be the front of the chair.
A block of wood will keep the bottom plywood and the chassis secure. I used some glue and two 3 inch screws on each side. It is important to first drill then put in the screws because the block is small and could split.
A carriage bolt, nut and washers will hold the steering together.
The bottom of the cart
Testing it out in the shop
Conclusion
The hoverchair was actually a very easy build. A little bit of hardware and a few pieces of wood it cost me no more than $10.00. I had my own wheels but they can be found at a caster shop for around $10.00 each.
The chair works fine in the shop and outside I was able to take it to the end of the street a few times. If you have a hoverboard I hope these instructions can help you build one.
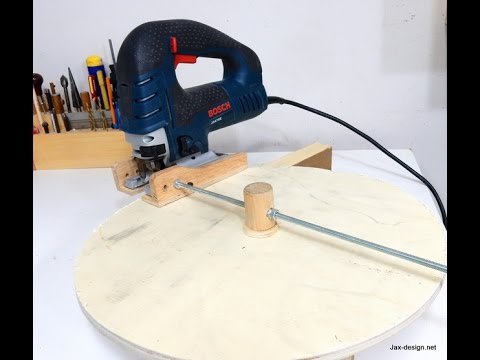
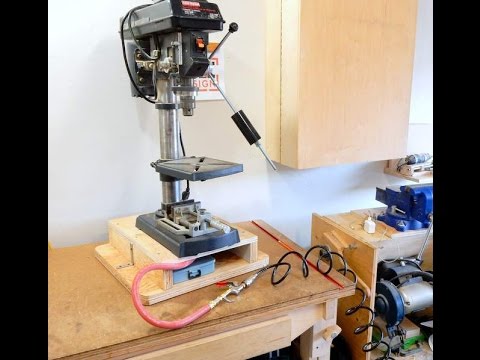
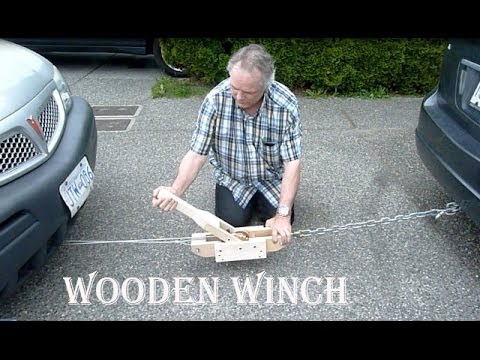