A compass is often used as a symbol of precision and discernment.
I like to use a compass for woodworking, the points
make it easy to get precise measurements and for
marking distances repeatably and very accurately.
How to Build a Large Wooden Compass !
To start I found nice piece of oak with some interesting grain, I will cut this for the legs. Since the compass will be large I will cut them to 13" in length. To get a clean cut I will use my table saw miter gauge .
On the table saw the pieces are cut into strips 5/16"x 1 1/8".
Prototype
I sometimes build a prototype to see if a project will work. I built the one shown here in about 15 minutes and was happy how it turned out, and know I was ready to build a larger one.
I will actually keep and use the smaller one because it works fine.
It will be another addition to my woodworking tools.
The strips of wood for the legs are marked and ready for the band saw and the drill press.
Cutting the shape on the band saw....
A small hole is drilled and a finishing nail is used as a center pin to make the hinge.
Since the hole is slightly smaller than the nail the nail should be carefully pounded in. A small drop of lubricant can be added so the parts move smoothly.
Time to drill the hole for the threaded rod. Since the piece is spring loaded a clamp should be used to secure the piece while drilling.
The same finishing nails for the hinge can be used for the compass points. I have moved the drill press table over and used a screw clamp to hold the piece secure. Use a small level or eyeball the leg to make sure it is vertical prior to drilling.
The head of the nails are cut off and pushed into the base of the legs with a pair of pump pliers.
A threaded rod is installed and a knurled brass nut is put on. A
couple of nuts are put on the ends to keep everything together.
This was a very simple woodworking project and one that I will
certainly use often. The reach is slightly over 1 foot. I really like
many different measuring tools and this one is a keeper. An easy
woodworking tool that can be made in less than 1 hour.
See Also:
Vacuum Hose Holder Make a Spray Can Rack Make a Dowel Stop Gauge
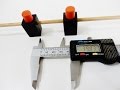
Prototype
I sometimes build a prototype to see if a project will work. I built the one shown here in about 15 minutes and was happy how it turned out, and know I was ready to build a larger one.
I will actually keep and use the smaller one because it works fine.
It will be another addition to my woodworking tools.
The strips of wood for the legs are marked and ready for the band saw and the drill press.
A small hole is drilled and a finishing nail is used as a center pin to make the hinge.
Since the hole is slightly smaller than the nail the nail should be carefully pounded in. A small drop of lubricant can be added so the parts move smoothly.
Time to drill the hole for the threaded rod. Since the piece is spring loaded a clamp should be used to secure the piece while drilling.
The same finishing nails for the hinge can be used for the compass points. I have moved the drill press table over and used a screw clamp to hold the piece secure. Use a small level or eyeball the leg to make sure it is vertical prior to drilling.
The head of the nails are cut off and pushed into the base of the legs with a pair of pump pliers.
couple of nuts are put on the ends to keep everything together.
This was a very simple woodworking project and one that I will
certainly use often. The reach is slightly over 1 foot. I really like
many different measuring tools and this one is a keeper. An easy
woodworking tool that can be made in less than 1 hour.
See Also:
Vacuum Hose Holder Make a Spray Can Rack Make a Dowel Stop Gauge


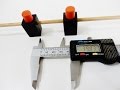